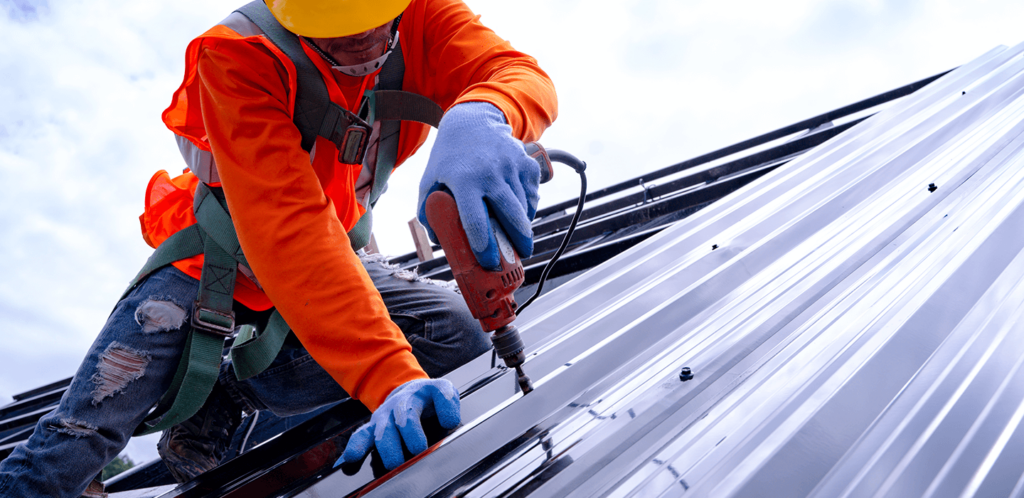
Houck
Blog
Through years of experience, Houck has become an expert in the most complex industrial, institutional, and commercial construction projects. However, we know there is always more to learn, and we encourage you to learn with us. Stay up-to-date on the latest Houck news and industry insights by reading our blogs.
- Houck News
Houck Group, Inc. Announces the Acquisition of Progressive Services Incorporated’s Business Assets
Houck Group, Inc. has announced the acquisition of the business assets of…
- Houck News
UPDATES ON COVID-19 FROM HOUCK
To our employees, business partners, vendors, community leaders, and friends, We hope…
- Concrete Restoration
Do I Need Concrete Restoration Services?
Concrete is a strong, versatile material, but it’s not indestructible. Damage and…
- Caulk Removal and Replacement
What to Know About Caulk Removal and Replacement
What to Know About Caulk Removal and Replacement Caulk removal and replacement…
- Roof Maintenance
What to Know About Waterproofing Your Rooftop
During harsh rainstorms, water can accumulate on your roof and seep through…
- Roof Maintenance
Re-Roofing Versus Roof Replacements
Is your roof nearing the end of its life? Whether you notice…
- Houck News
Houck Group, Inc. Announces the Acquisition of Progressive Services Incorporated’s Business Assets
Houck Group, Inc. has announced the acquisition of the business assets of…
- Houck News
UPDATES ON COVID-19 FROM HOUCK
To our employees, business partners, vendors, community leaders, and friends, We hope…
- Commercial Contractor
How To Select A Specialized Commercial Contractor
When it comes to selecting a quality, specialty contractor for your facility,…
- Roof Maintenance
Roof Replacement: What You Need to Know
Everything You Should Know About Roof Replacements If it’s time for your…
- Industry News
What Are Risk Assessments and Factors in Construction?
You have the right to expect your workplace to be safe and…
- Industry News
Trends That Are Poised to Impact Construction
Construction is a dynamic field, and upcoming advances will noticeably shift many…